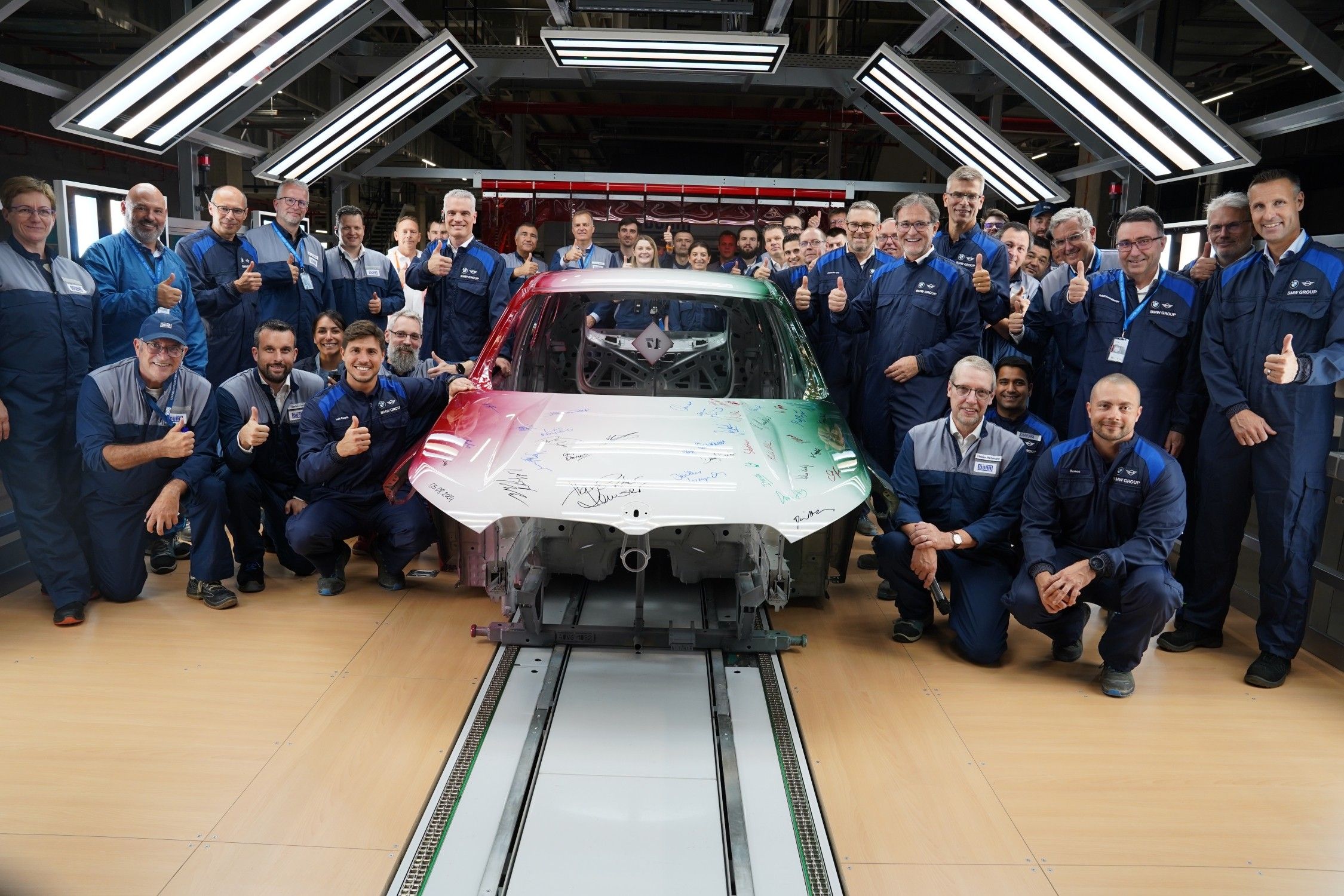
BMW Group Plant Debrecen: Leading the Future of Sustainable Automotive Production
The BMW Group's new Plant Debrecen in Hungary is rapidly taking shape, setting new standards in sustainable automotive production. As the first technology to be commissioned at this state-of-the-art facility, the paint shop exemplifies BMW's commitment to environmental responsibility and innovation. By leveraging groundbreaking processes and systems such as power-to-heat, Heat Grid, and eRTO, this plant is on track to become the first in the BMW Group's global production network to operate entirely without fossil fuels. This pioneering approach not only reflects BMW's dedication to sustainability but also provides a blueprint for all future BMW iFACTORY plants.
History and Vision Behind BMW Plant Debrecen
BMW's vision for the Debrecen plant aligns with its broader goal of leading the automotive industry toward a greener future. The plant is integral to the production of BMW's Neue Klasse, a new generation of vehicles that will incorporate advanced technologies and sustainable practices. Scheduled to commence pre-series production by the end of the year, the Debrecen facility is a milestone in BMW's journey towards reducing its carbon footprint and achieving greater efficiency in its operations.
Cutting-Edge Technology and Environmental Responsibility
The new paint shop at Plant Debrecen is designed to handle the high-volume production demands of modern automotive manufacturing while maintaining an environmentally friendly operation. Capable of painting 30 vehicle bodies per hour, the system is fully automated and can significantly increase capacity as needed. The advanced design and technology employed in this 33,000-square-meter facility demonstrate BMW's commitment to combining efficiency with sustainability.
Power-to-Heat: A Game-Changer in Reducing Carbon Footprint
One of the most innovative aspects of the Debrecen paint shop is the power-to-heat system, which eliminates the need for fossil fuels like natural gas. By relying solely on electricity, the paint shop drastically reduces its carbon footprint, even though this transition results in higher electricity consumption. However, the power used at the Debrecen facility is sourced exclusively from renewable energy, further emphasizing BMW's dedication to sustainable production.
Heat Grid: Enhancing Energy Efficiency
The Heat Grid project is another key innovation at the Debrecen plant, offering an additional ten percent in energy savings. This project involves recovering waste heat from various processes and using it to preheat water for the facility. The entire system operates at a lower temperature than previous installations, significantly reducing energy consumption while maintaining optimal conditions in the paint shop.
eRTO: Advanced Exhaust Purification
In an industry first, the Debrecen plant uses the eRTO (electric regenerative thermal oxidation) process for exhaust purification. This innovative system efficiently purifies exhaust air using electricity, achieving high energy efficiency through its superior thermal recovery capabilities. The eRTO process represents a significant advancement in reducing the environmental impact of automotive manufacturing.
Modern Dry Separation Technology
In line with BMW's commitment to reducing environmental impact, the Debrecen paint shop utilizes dry separation technology to handle paint overspray. This method reduces water consumption and allows for the recirculation of air within the spray booth, resulting in significant energy savings. The reused limestone powder further exemplifies BMW's focus on sustainability, contributing to a closed-loop system that minimizes waste.
Digitalization and Automation: The Future of Automotive Production
The comprehensive digitalization of the Debrecen paint shop ensures high efficiency and precision. Automated Guided Vehicles (AGVs) seamlessly transport car bodies through the production process, while Automated Surface Inspection (AOI) uses artificial intelligence to detect and address any irregularities post-painting. These technologies, combined with virtual planning and training, position Plant Debrecen at the forefront of modern automotive manufacturing.
Conclusion: A Blueprint for the Future
The BMW Group Plant Debrecen stands as a testament to the future of automotive production, where sustainability, efficiency, and innovation converge. As the first paint shop in the BMW Group's global network to operate entirely without fossil fuels, it sets a new benchmark for the industry. This facility not only represents the next step in BMW's journey toward sustainable luxury but also offers valuable insights into the future of automotive manufacturing.
For those in the UAE interested in exploring the latest in automotive innovation, including the potential future availability of vehicles produced at the Debrecen plant, visit Auto Trader UAE. Here, you can find a wide range of used cars for sale in Dubai and across the UAE, offering the perfect blend of luxury, performance, and cutting-edge technology.